
Industrial
DIGITAL ENGINEERING AND EVALUATION
Dynamic evaluation of industrial drive systems
Dynamic evaluation of industrial drive systems involves directly accounting for irregularities stemming from the motor or load unit, and analyzing transient operating conditions. It includes the detection and "detuning" of torsional drive vibration and belt flapping, necessitating dynamic belt parameters. The process utilizes empirical borderline values for drive evaluation and conducts a detailed assessment of noise, vibration, and harshness (NVH), along with stress results. Moreover, it encompasses the evaluation of comprehensive dynamic results, incorporating integrated feedback.
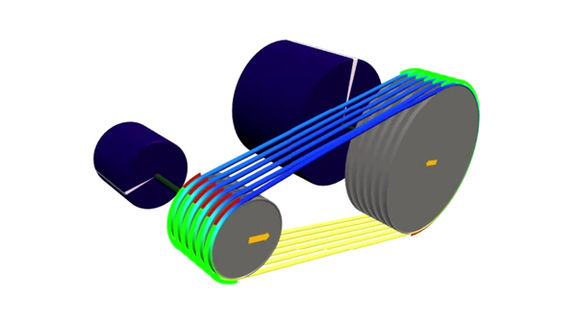
E-Motor Piston Compressor
High compressor torque irregularities:
Problem: Critical belt flapping
Task: Find a configuration with reduced belt flapping in the entire speed and load range
Challenge:
-
Dominating torque irregularities from compressor
-
E-motor requires a torque based speed control (fixed speed excitation detunes the system)
E-Bike Drive
High tooth load after increasing the system power
Problem: Reduced belt life caused by tooth cracking
Task: Suggestion of design changes to reduce tooth load and wear
Load:
-
Static
Challenge:
-
Unequally distributed tooth forces on the driver sprocket Force transmission by friction and tooth force
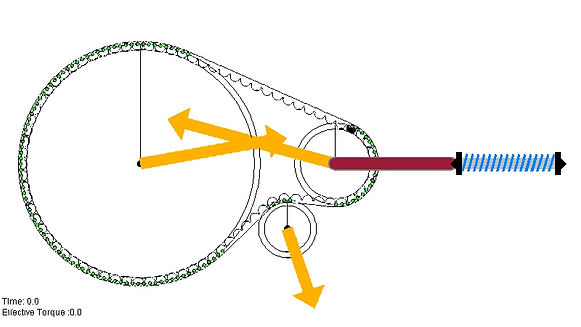
Packing Machine
Oscillating inertia driven loads:
Problem: Understanding the belt durability differences in layout variants
Task: Optimization of drive parameters to reduce tooth wear
Excitation:
-
Oscillating inertia driven loads, Implementation of a ‘Inertia-Variator element’ to replicate the complex kinematic system by reading the customers inertia characteristic
Motor setup:
-
Detailed motor and controller model based on data sheets and customer performance tests
E-Power Steering Unit
Belt vibrations
Problem: Structural NVH issues
Task: Understanding the design changing effects to the systems NVH behavior
-
Craig Bampton Reduction for the housing to replicate the accelerometer results at certain mount points
-
Functional mock up unit (FMU) to integrate the steering control as “black box” into the MBS software
-
Simulation of maximum steering force operations (left/right)
-
Belt and engine as source of vibrations, bearings, coupling stiffnesses, clearances and the housing as a complex non-linear transfer path and resonator
