
Driving Performance Simulation
DIGITAL ENGINEERING AND EVALUATION
Complete Vehicle Simulation
Overall system simulations have become crucial in the early stages of design, despite the challenge of needing detailed model parameters and data maps that typically come from later experiments. A significant advancement in this area is the development of virtual 3D validation models at the system level. These models offer high predictive accuracy and can fully substitute for physical testing. They provide all necessary input data and parameters for a 1D vehicle model through a standardized interface. These simulations can be applied in a variety of scenarios, including:
-
Starting the engine, lugging, change of mind, braking, gear up-shifting, and down-shifting with clutch engagement.
-
Performance analysis, such as acceleration tests and range estimation.
-
Simulation of different driving conditions, including uphill, downhill, urban, and rural environments.
-
Optimization of operational strategies, enhancing vehicle range and reducing fuel consumption.



Driving performance simulation
ICEV:
-
Acceleration simulation ICEV
-
Velocity: 194km/h
-
Tire – road contact:
-
Critical stick area for gear 1
-
(max Power)
​
PHEV 4x4:
-
Acceleration simulation PHEV4x4
-
Max Velocity : 256km/h
-
Tire – road contact:
-
Critical stick area for gear 1
-
front and rear axle
​
BEV:
-
Acceleration simulation BEV
-
Max Velocity: 188km/h
-
Tire – road contact:
-
Critical stick behavior for low velocity
-
Battery power limited to 100 kW - maximum possible acceleration is not reached
BEV Cycle simulation
-
Vehicle weight used: 1250kg
-
1 gear transmission with 2 ratios:
-
Main gear stage (29/53) + differential (20/69) total gear ratio: 6.31
-
Efficiency map of electric machine and transmission in use
-
SOC status determined via battery model
-
Simulation time for the entire system: < 50min
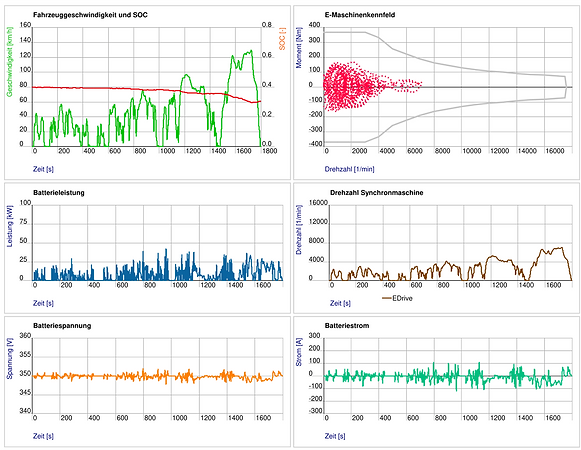