
ICE & Hybrid
DIGITAL ENGINEERING AND EVALUATION
ICE
Optimize internal combustion engine development with our all-in-one modular simulation solution. Our advanced 3D Multi-Body Simulation (MBS) model accurately represents each component, crucial for partners and suppliers to understand specific loads and conditions. This modularity enables easy separation and optimization of subsystems, utilizing fast calculation models for efficient enhancements. Post-optimization, subsystems are seamlessly reintegrated into the 3D MBS for thorough testing and validation, ensuring all changes are perfectly aligned.


The Digital Twin generated from this process is a cornerstone for predicting dynamic system behavior, mastering Noise, Vibration, and Harshness (NVH), and evaluating engine acoustics. This platform fosters a collaborative environment between Original Equipment Manufacturers (OEMs) and suppliers, streamlining the development process, and leading to more effective and efficient engine designs.
Use cases in ICE development
Hybrid
The expansion of conventional to electromechanical vehicle drives is a consequence of the demand for environmentally friendly mobility with optimized energy management. This is achieved through the combination of internal combustion engine and electric drive components and places high demands on the system architecture.
The design process account for both detailed drive design using 3D (full-order) models and evaluation in driving cycles using reduced order models based on data directly derived from the full-order models within SIMDRIVE3D.

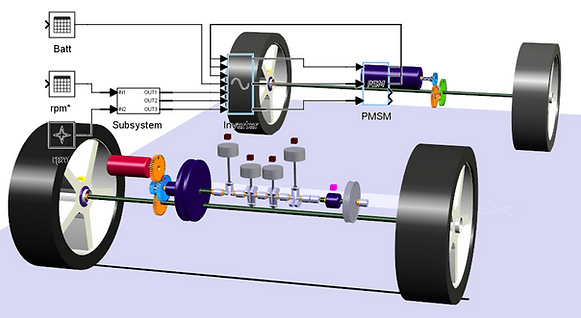
In order to be able to design the different design requirements from the mechanical and electrical system simultaneously, a multidisciplinary simulation approach is pursued that includes the control units and magnetic forces in order to design the resulting different design requirements simultaneously and thus shorten development cycles.
The objective of complete hybrid drive simulations is the determination of driving dynamics and NVH for different driving cycles and manoeuvres while shafts and rotor stresses, dynamic bearing loads, gear noise and vibrations must be kept within certain limiting values.
With this approach, there are no limits in terms of flexibility and expandability in order to be able to detail the vehicle models for further analyses.